Ultrasonic Testing Non-destructive testing (NDT) is essential for assessing the integrity of materials without causing damage.
Among various NDT techniques, ultrasonic testing is widely used to detect internal flaws, measure material thickness, and evaluate weld quality.
This blog explores how ultrasonic testing works, its applications in different industries, its advantages, and potential limitations.
What is NDT Ultrasonic Testing
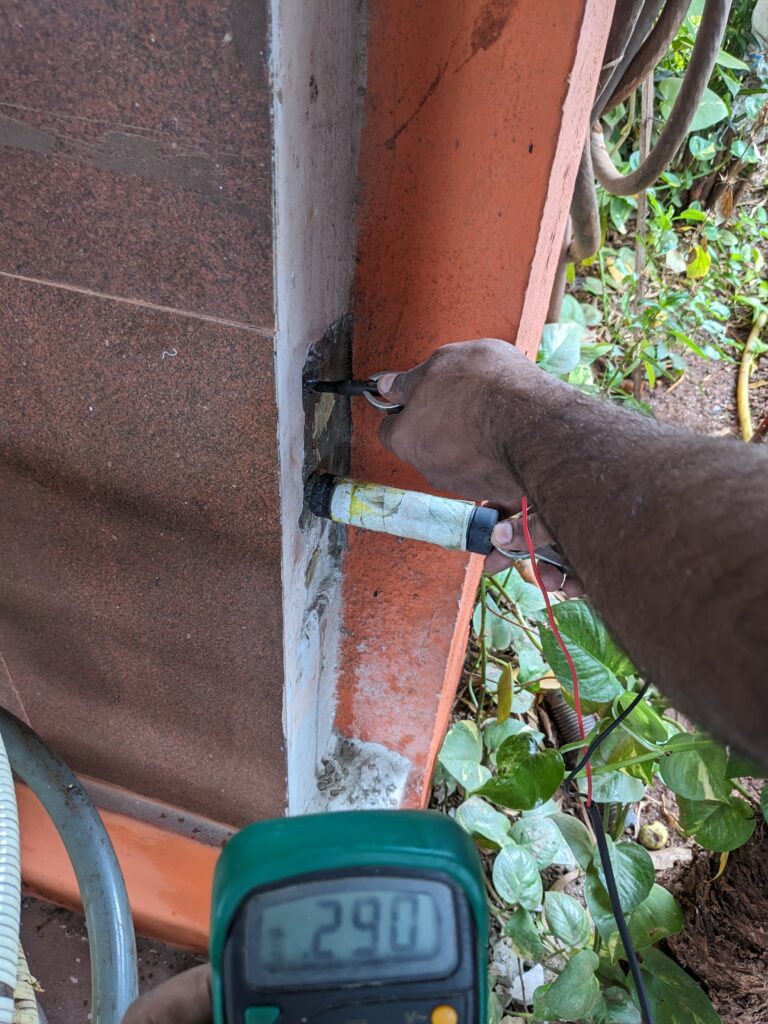
Ultrasonic testing (UT) is a method used to inspect materials for internal defects using high-frequency sound waves.
It is non-invasive and highly reliable for detecting cracks, voids, and discontinuities in metals, composites, and other materials.
This technique is widely used in industries like construction, aerospace, manufacturing, and oil & gas.
It helps ensure structural safety, enhances product reliability, and reduces the risk of material failure.
How Does Ultrasonic Testing Work?
Ultrasonic testing involves sending high-frequency sound waves into a material.
These waves travel through the material until they encounter a boundary, such as a crack or void.
When this happens, part of the wave reflects back and is detected by a receiver.
By analyzing the time taken for the echoes to return, inspectors can determine the depth, size, and nature of any flaws.
This makes ultrasonic testing a powerful tool for assessing material integrity.
Key Components of Ultrasonic Testing Equipment
- Transducer: Converts electrical energy into ultrasonic waves.
- Pulser/Receiver: Generates and receives sound waves.
- Display Unit: Shows the reflected signals for analysis.
- Coupland: A gel or liquid applied to enhance sound wave transmission.
Principles of Sound Wave Propagation in Ultrasonic Testing
Sound waves travel differently depending on the medium.
They can reflect, refract, or get absorbed, affecting how flaws are detected.
Understanding these principles is crucial for accurate ultrasonic testing.
Applications of Ultrasonic Testing in Various Industries
Ultrasonic Testing in the Construction Industry
Ultrasonic testing is used to assess the integrity of concrete, steel structures, and bridges.
It helps in detecting internal defects, voids, and cracks that are not visible externally.
By using UT, engineers can ensure the structural soundness of buildings, avoiding potential failures.
Role of Ultrasonic Inspection in Aerospace Engineering
Aircraft components must meet strict safety standards.
Ultrasonic testing is used to inspect turbine blades, fuselage structures, and composite materials.
It helps detect fatigue cracks and manufacturing defects, ensuring aircraft safety.
Importance of Ultrasonic Testing in Pipeline and Weld Inspections
Oil & gas pipelines must be free from defects to prevent leaks and failures.
Ultrasonic testing is used to inspect welds, detect corrosion, and measure pipeline thickness. This ensures compliance with industry safety regulations and extends the lifespan of pipelines
Advantages of Ultrasonic Testing Over Other NDT Methods
- High Sensitivity: Can detect even the smallest defects.
- Accurate Depth Measurement: Determines the exact location of flaws.
- Non-Destructive: Does not damage the material being tested.
- Portable Equipment: Can be used in various environments.
Fast and Efficient: Provides instant results with minimal downtime
Challenges and Limitations of Ultrasonic Testing
- Surface Preparation Required: Testing requires a clean and smooth surface.
- Operator Skill-Dependent: Results depend on the expertise of the technician.
- Limited for Complex Geometries: Curved or irregular surfaces can be difficult to inspect.
Coupland Required: A liquid medium is necessary for sound transmission
Conclusion
Ultrasonic testing is a reliable, efficient, and widely used NDT method.
It plays a crucial role in ensuring material integrity across multiple industries.
While it has some limitations, its advantages make it indispensable for structural safety and quality assurance.
For industries looking to maintain high safety standards, ultrasonic testing remains one of the best NDT solutions available.
- The Cost of Ignoring Structural Audits: Risks Every Society Must Know
- Key Machines Used by Structural Auditors in Mumbai
- Rebound Hammer Test: A Key NDT Method in Structural Audit
- When Does a Building Qualify for Redevelopment?
- Structural Audit: Real Insight into a Building’s Health Report
- Redevelopment vs Self-Redevelopment After Structural Audit: What Housing Societies Must Know
- Why Core Test NDT Testing is Important in Structural Audit
- Half Cell Potential Test – A Key Method in Structural Audits
- Understanding Ultrasonic Testing NDT: Uses and Key Details
- Structural Audit – What Happens If We Do Not Conduct a Structural Audit of Our Building?
- The Major Problems of Not Conducting a Structural Audit
- Have You Done a Structural Audit of Your Building?
- Non-Destructive Testing (NDT) in Structural Audits: A Comprehensive Guide
- The Essential Role of Structural Auditors in Redevelopment
- Is Your Building Safe? Top Warning Signs Structural Audits Can Detect!
- how structural audit helps to solve building Foundation issues
- The Role of Non-Destructive Testing in Structural Audits
- Understanding the Structural Audit of Commercial Buildings